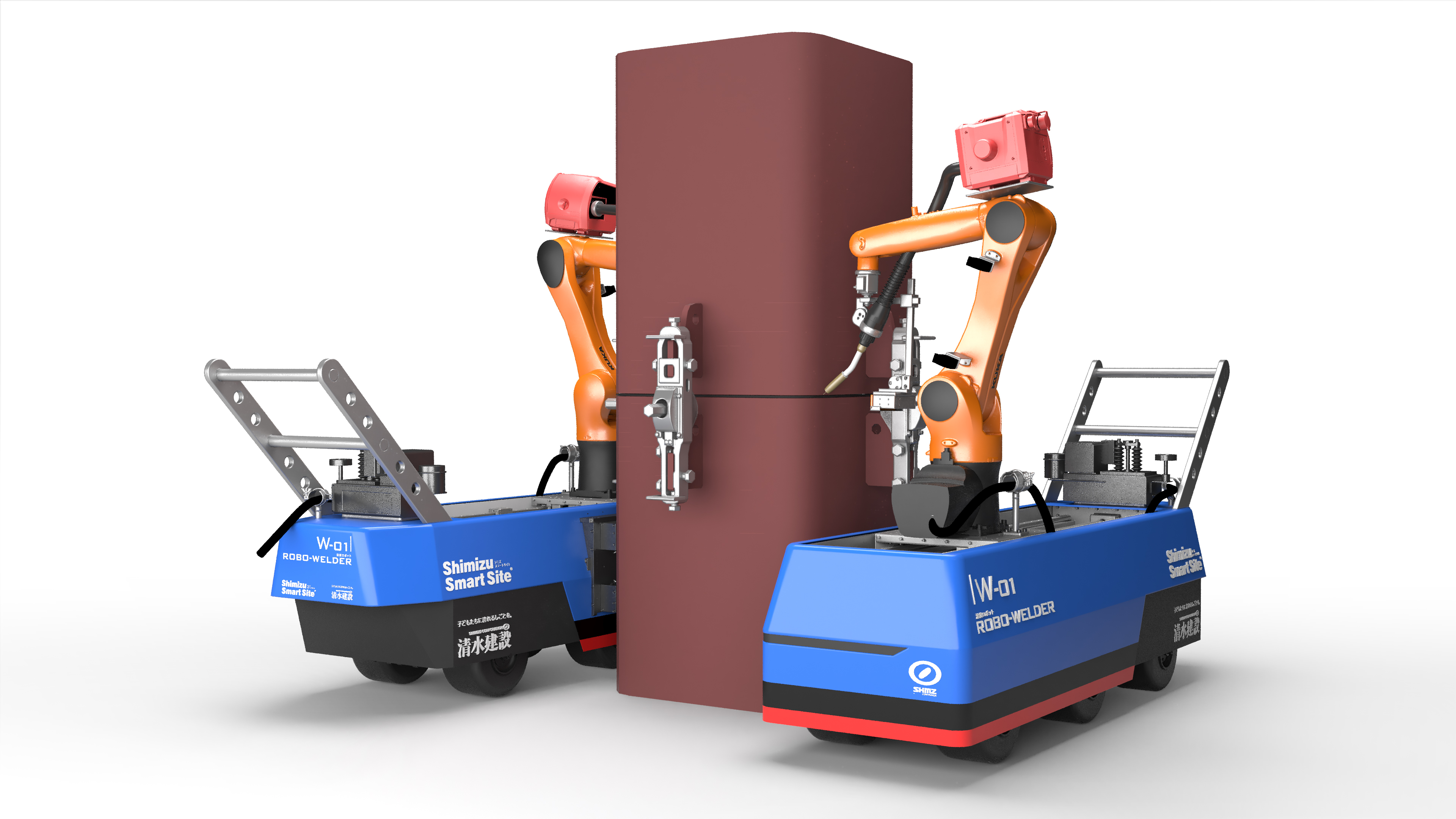
As we fret over the large exodus of skilled technical workers, we seek to build a forward-thinking production system where autonomous robots outfitted with Shimizu's state-of-the-art technology collaborate with humans to carry forward construction projects. This ambition drives our development of construction robots. As part of this effort, we have opened a construction robot laboratory inside our Institute of Technology that is now fully up and running.
The main robots that will be in charge of the Shimz Smart Site, our company's idea for a next-generation production system, are now being taught inside the laboratory before full-scale operations commence at the Site this fall. When you see the Robo-Welder welding steel columns, the Robo-Buddy installing ceiling boards and floorboards, and the Robo-Carrier transporting supplies, we believe you will get a sense of the construction site of the future.
We will provide the media with a tour of the construction robot laboratory as detailed below, so we certainly hope you will join us.
≪Details≫
1. Date/time: 1:30 – 3:00 p.m. on Monday, April 23, 2018
2. Place: Shimizu Corporation Institute of Technology
3-4-17 Etchujima, Koto-ku Tel: 03-3820-5504
https://www.shimz.co.jp/en/company/about/sit/access/
・10 minutes from Etchujima Station (JR Keiyo Line)
・15 to 20 minutes from Monzennakacho Station (Tokyo Metro Tozai Line, Toei Oedo Line)
・15 minutes from Toyosu Station (Tokyo Metro Yurakucho Line, Yurikamome Line)
3. Sessions: Briefing on robots' features (20 min.)
Tour (50 min.)
Q&A (20 min.)
4. Note: Due to the nature of the venue, we ask that would-be participants fill out the required items in the application form on the following page and send it by either fax or email by 19th of April.
Fax: 03-3561-8527 Email: hideo@shimz.co.jp
An interpreter(Japanese・English) will be present.
<Application Form>
Company:
Name:
Phone #:
Mobile #:
Email:
For inquiries concerning this matter, please contact Imamura or Noguchi at the Corporate Communication Dept. (Tel: 03-3561-1186).
≪Reference≫
■ Robo-Welder
Once Robo-Welder has been placed on a special conveyor and is guided to the designated position, it automatically performs all welding without worker intervention. The robot recognizes the channel shape (groove) of the spot to be welded by laser measurement. A robotic arm equipped with a welding torch moves freely along six axes and determines the conditions in real-time for accurately welding the groove with welding material. The welding work uses two robots. We also plan to introduce a non-contact system that can inspect the quality of welded components in real time.
■ Robo-Buddy
Robo-Buddy recognizes its own position via laser sensors and referencing BIM information (SLAM function), and automatically moves to the specified work location. It is also equipped with a special feature that enables it to climb over level differences of 20 cm. The two robot arms that perform the work move freely along six axes and can pick up materials weighing up to 30 kg. It operates on an elevating pedestal on top of an automatic guided vehicle. After it recognizes the location to perform the work via imaging sensors and laser sensors, it uses its two robotic arms to insert ceiling suspension bolts, assemble the base materials, and install the ceiling board, screw it into place, and install the OA floor pedestal and paneling. This robot can be used to perform multiple functions by switching the end effectors at the tip of the robotic arms.
■ Robo-Carrier
Robo-Carrier is the automatic conveyor system that transports the materials delivered to the job site to the location where Robo-Buddy will perform its work. Robo-Carrier recognizes its own position via laser sensors and referencing BIM information, and automatically transports materials to the designated work site. When it encounters an obstacle, it performs a repeat search and corrects course. The Robo-Carrier is deployed on ground level and loads palletized materials on an Autonomous ELV that works in concert with it. When the ELV arrives at the delivery destination, another Robo-Carrier unloads each pallet from the ELV and transports it to the temporary staging area. The Robo-Fork loads the materials in the temporary staging area onto the Robo-Assist which works alongside the Robo-Buddy and carries them to the Robo-Buddy base.