Date : January 29 - 30, 2025
Fukushima Innovation Coast Framework Press Tour
post date : 2025.01.06
Fukushima Innovation Coast Framework Press Tour
Tour Dates: Wednesday, January 29–Thursday, January 30, 2025
A development center for advanced technology in Fukushima:
Reconstruction and beyond
- Rocket launches, next-generation transportation, self-healing concrete, Muscle Suits exoskeletons, and plant factories
- College of technology training students for the decommissioning of the Fukushima Daiichi Nuclear Power Station
[Tour Details]
March 14, 2025 will mark 14 years since the Great East Japan Earthquake. In Fukushima Prefecture’s coastal area (Hamadori), which suffered major damage, a research and development center for innovative technology is being built under the Fukushima Innovation Coast Framework, a national project to build a new foundation for industry in the area.
The Fukushima Innovation Coast Framework is a national project to rebuild the industry Fukushima Prefecture’s Hamadori and neighboring areas lost due to the Great East Japan Earthquake and the nuclear disaster, providing support to businesses such as subsidies and test facilities for R&D and focusing on six key fields: decommissioning; robotics and drones; energy, environment, and recycling; agriculture, forestry, and fisheries; medicine; and aerospace.
Through this framework, startups and other businesses from around Japan have been gathering in municipalities around Hamadori, where tests are carried out daily on next-generation technologies in various fields, and it has been receiving attention as the frontline for innovation in Japan. By cultivating new technologies and businesses in this area, it is hoped it will contribute not only to recovery from the disaster, but also to sustainable development of the region.
◆This press tour will cover companies in the Fukushima Prefecture Hamadori area carrying out production and R&D of unique technologies under the Fukushima Innovation Coast Framework, as well as speaking with students at a local college of technology that is focusing on training students for decommissioning the Fukushima Daiichi Nuclear Power Station.
1. Fukushima Robot Test Field (Minamisoma)
—A R&D center unique in the world providing land, sea, and air testing environments
The Fukushima Robot Test Field (RTF) fully opened in March 2020 and spans approximately 1,000 meters east to west and 500 meters north to south. The field has an unmanned aircraft (drone) area, an infrastructure inspection and disaster response area, an underwater and marine robot area, and a development base area, making it a research and development center unique in the world where various robots for land, sea, and air can be tested. There are offices for around 20 companies in the RTF, and its facilities are used approximately 5,000 times each year.
◆At the Fukushima Robot Test Field, the tour will hear an overview of the Fukushima Innovation Coast framework, the project’s goals, and specific initiatives from Fukushima Innovation Coast Promotion Organization staff.
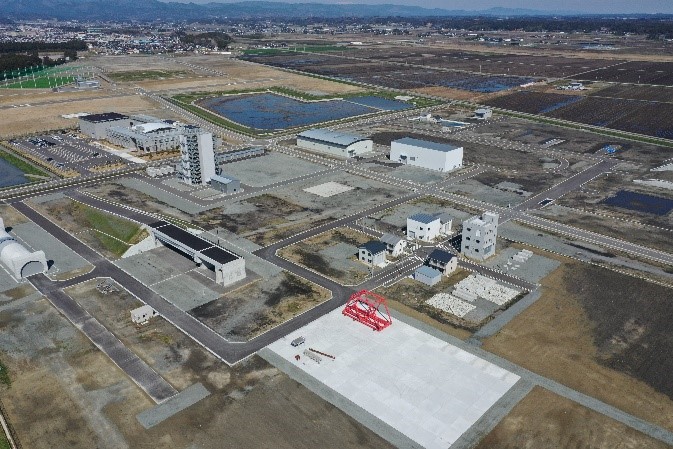
【Photo courtesy of Fukushima Innovation Coast Promotion Organization】
2. AstroX, Inc. (Minamisoma)
—Aiming for “Japan as No. 1” in space development with a revolutionary rocket launch method
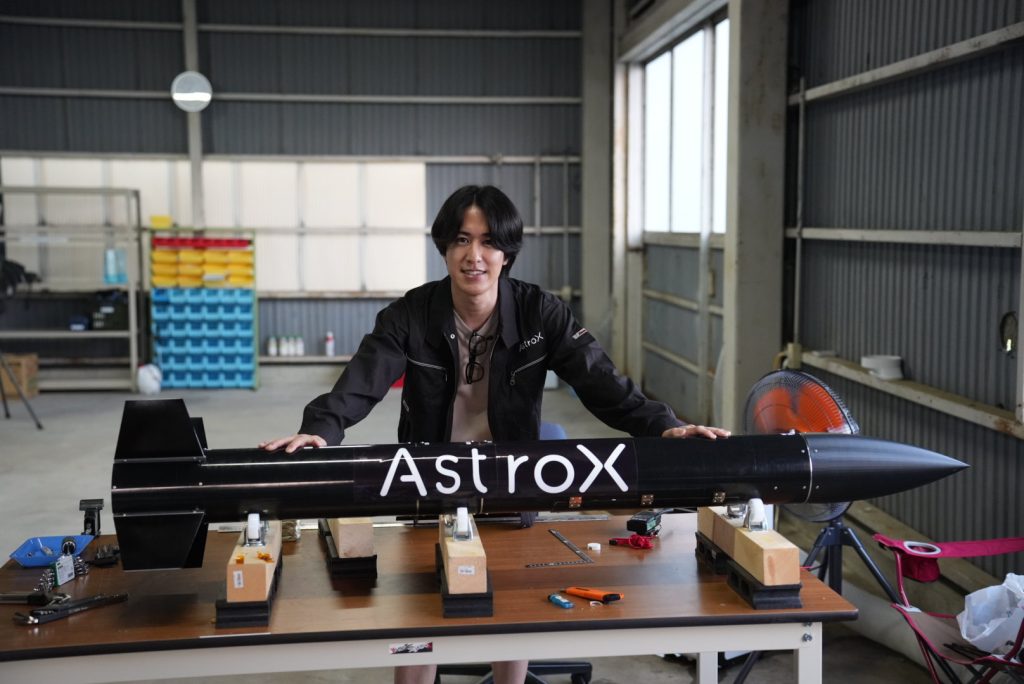
【Photo courtesy of AstroX, Inc.】
AstroX, Inc. is an aerospace startup established in 2022 by Mr. Shobu Oda, who previously ran an IT company, with the vision of having “Japan as No. 1” again, this time in space development.
AstroX is researching Rockoon (rocket + balloon) launch technology, an unprecedented launch method which uses a balloon to carry a rocket to the stratosphere, from where it is then air launched, and they have taken the lead over other companies worldwide in research to make the technology practical.
With an attitude control device developed by AstroX to maintain the proper orientation, it is possible to significantly decrease air resistance by air launching a rocket from the stratosphere at an altitude of approximately 20 km. This allows highly efficient launches for one third of the cost of existing methods. Since a dedicated launchpad is not needed for the launch either, according to AstroX’s CEO Mr. Oda there has been significant interest from overseas as well, in areas such as Europe where launch sites are limited.
In November 2024, in Minamisoma, Fukushima, AstroX successfully performed a test launch from the ground of a hybrid rocket (with a diameter of approximately 6 meters) using solid fuel and a liquid oxidizer for propellant, to an altitude of 10 km. In FY 2025, they are aiming to reach space at an altitude of 100 km, and plan to establish the Rockoon technology by 2029, before opening a business to launch satellites in the early 2030s. By doing so, they intend to solve the supply shortage of rockets to launch satellites which is an issue for space development in Japan.
Mr. Oda said the main reasons they chose to develop their rocket launch technology in Fukushima was due to the quick turnaround by the local government and the tangible and intangible support they can receive, as well as the locals creating an atmosphere of support for space businesses. AstroX is carrying out R&D while taking full advantage of the strengths of Fukushima’s environment, and it is hoped the company will drive the future of the Japanese space industry from Fukushima.
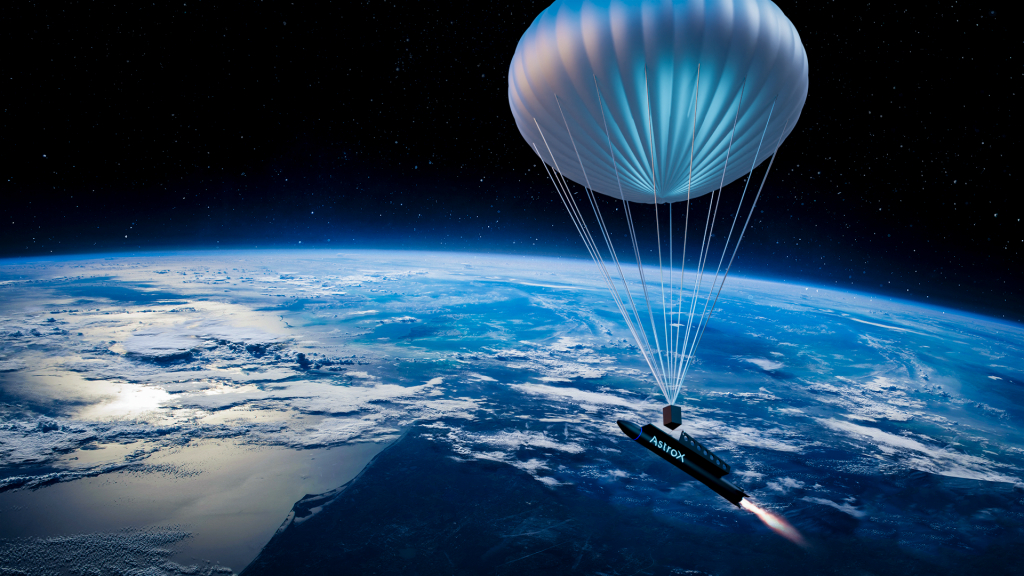
【Photo courtesy of AstroX, Inc.】
◆The tour will visit AstroX’s rocket development plant and see the compact rocket Kogitsune which was used in an August 2024 launch test, as well as the attitude control device used for air launches, and hear from AstroX CEO Mr. Shobu Oda about his vision for the future of private-sector space development in Japan.
3. Zip Infrastructure, Inc. (Minamisoma)
—Aiming to solve traffic congestion in urban areas with self-driven cable cars
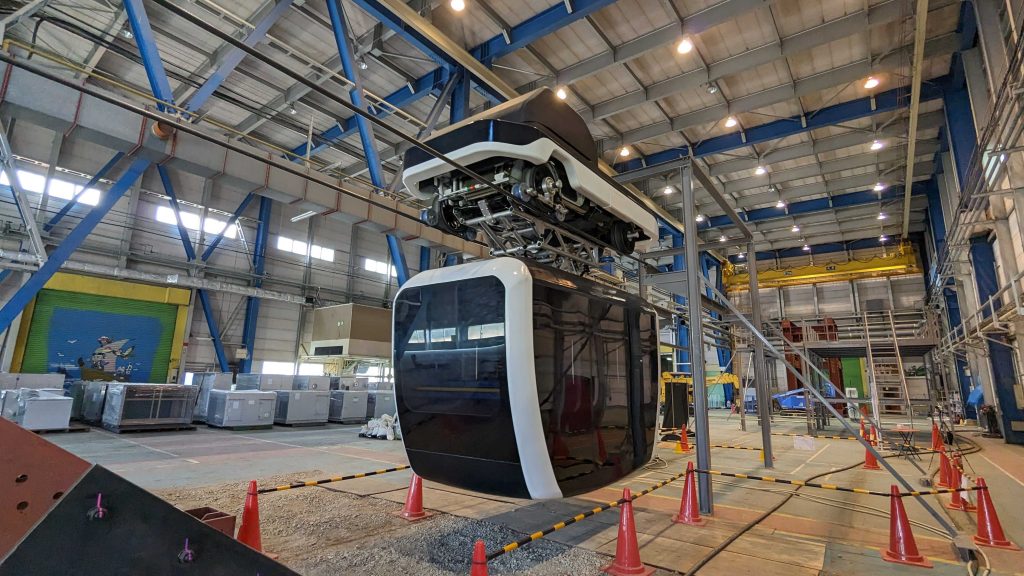
【Photo courtesy of Zip Infrastructure, Inc.】
*On the day of the tour, it will only be possible to see the gondola part of Zippar, not the cable. Be aware it will not be possible to take a photo like the one above.
Zip Infrastructure, Inc. is a startup that has developed a new transportation system called Zippar, a self-driven cable car system, with the goal of solving the issue of traffic congestion, which is becoming more severe in urban areas throughout the world. The company was founded in 2018 by Mr. Takamasa Suchi, who while in university researched space elevators (a vision connecting Earth and space with cables, and using them to transport people and goods).
Zippar, the self-driven cable car system developed by Zip Infrastructure, costs 1.5 billion yen per km, approximately one fifth of the cost for monorail, and the design and construction can be completed quickly in about one year each, so it is gaining attention as something that could revolutionize urban transportation. Since the cables and gondolas are independent from each other, unlike normal cable cars which can only move in a straight line, curves and branches can be included in the design to allow for high-frequency and flexible line operation. With unmanned operation, the system also solves the issue of a lack of operators. Since it does not require large columns to be constructed, it also has a low environmental burden.
Zip Infrastructure has already entered into memorandums of understanding with not only local governments in Japan, but also with the Bases Conversion and Development Authority (BCDA) in the Philippines, to carry out feasibility studies for implementing Zippar, and there are hopes from within Japan and abroad that it will solve traffic congestion in urban areas.
With its head office in Minamisoma, Fukushima, Zip Infrastructure was selected as one of the businesses to receive Fukushima Prefecture’s FY 2023 Regional Reconstruction Practical Application Development Promotion Subsidy, and currently they have built a test line for Zippar in the Fukushima Robot Test Field and are accelerating their R&D towards practical application.
◆The tour will visit the Fukushima head office of Zip Infrastructure, Inc. and see the gondola portion of the Zippar self-driven cable car, and hear from Zip Infrastructure’s COO, Mr. Mario Ian Carlos Ferido Rebonquin about progress towards practical application of the next-generation transportation system Zippar and its future outlook.
4. Kikuchi Seisakusho Co., Ltd. Minamisoma Factory (Minamisoma)
—An SME based out of Fukushima supporting startups with technological prowess. Also contributing to the mass production of Muscle Suit exoskeletons
Kikuchi Seisakusho Co., Ltd., an SME with approximately 300 employees founded in 1970, possesses advanced technology such as metal mold design/fabrication and sheet metal processing, and provides manufacturers in a variety of fields with support for developing new products, including everything from designing and producing molds to prototyping, evaluation, and mass production.
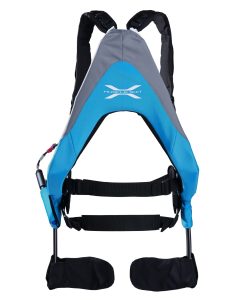
【Photo courtesy of Innophys Co., Ltd.】
Kikuchi Seisakusho also actively provides support to university spinoffs and other startups. In addition to investment, they use their expertise in processing technology and production to provide total support from development to mass production and sales, promoting the growth of startups while also growing the Kikuchi Seisakusho Group as a whole.
Kikuchi Seisakusho’s founder, president and CEO Mr. Isao Kikuchi is from Iitate, Fukushima, and with contributing to the region also being a goal, the company has nine factories in Fukushima Prefecture. One of these factories, the Minamisoma Factory, began operations in 2015 and is the headquarters for Kikuchi Seisakusho’s robotics business. Nineteen businesses supported by Kikuchi Seisakusho are carrying out R&D and production of robots and related products at the Minamisoma Factory, also contributing to job creation.
One example of a business they supported is the university spinoff Innophys Co., Ltd. Innophys applied artificial muscle technology to develop the Muscle Suit exoskeleton which laborers can wear to support their movements. Innophys was able to commatialize this and achieve mass production with support from Kikuchi Seisakusho. Innophys then expanded the business both domestically and overseas, and as of 2024 have sold over 30,000 Muscle Suits. Currently, they are available in 21 countries, mainly in Europe but also in Asia and Central and South America.

【Photo courtesy of Innophys Co., Ltd.】
◆The tour will visit the Kikuchi Seisakusho Co., Ltd. Minamisoma Factory and hear from Mr. Naotaka Otogawa, a board director of Kikuchi Seisakusho and representative director, president and CEO of Innophys Co., Ltd., about Kikuchi Seisakusho’s support for startups and the background behind the establishment of the Minamisoma Factory.
The tour will also be able to see where products are developed and manufactured in the factory. There will also be an explanation about the Innophys Muscle Suit, and an opportunity to wear a Muscle Suit to experience its effects firsthand.
5. Aizawa Concrete Co. (Namie)
—The first to succeed at establishing mass production for self-healing concrete that repairs its own cracks with the power of bacteria. A drastic increase in the lifespan of structures
Aizawa Concrete Co., founded in 1935, established the Fukushima RDM (Research/Development/Manufacturing) Center in Namie, Fukushima in 2023, and is gaining attention for its R&D production center with advanced technology coming from an area affected by disaster.
Aizawa Concrete jointly developed self-healing concrete technology with the Netherlands’ Delft University of Technology, and was the first in the world to succeed in establishing a method for its mass production.
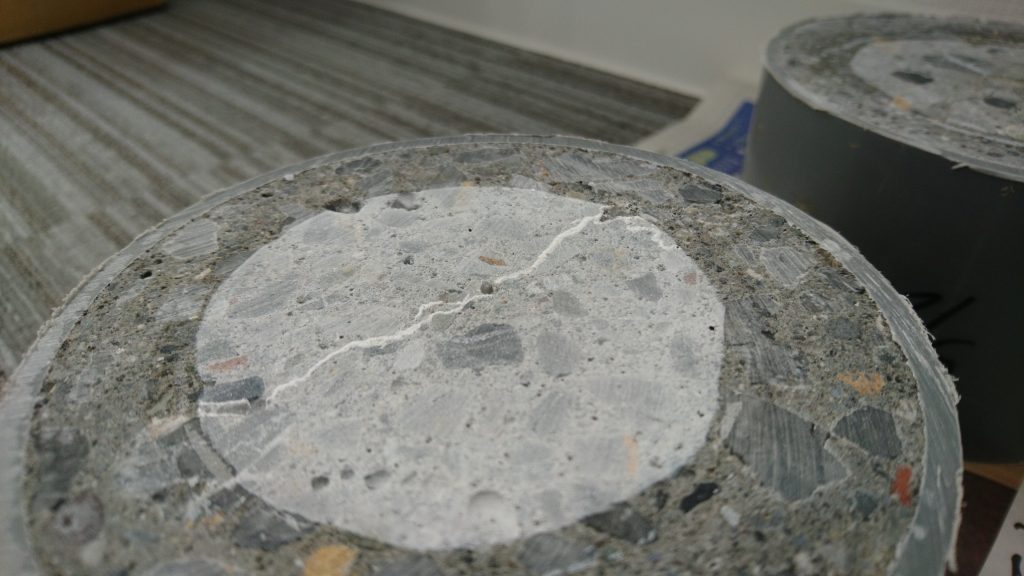
Sample concrete with a crack being healed by the metabolic functions of bacteria 【Photo courtesy of Aizawa Concrete, Co.】
When added to fresh concrete, the Basilisk Self-Healing Concrete Healing Agent produced by Aizawa Concrete, which has specially cultured alkaline resistant bacteria, will make it possible for cracks that occur to continuously repair themselves automatically, making it a revolutionary material.
In contrast to structures made with existing concrete products which had a lifespan of 60 to 70 years, structures made with Basilisk have a lifespan of over 100 years, providing incredible durability and lifespan. Since the large amounts of carbon dioxide produced when making concrete have become a major problem, Basilisk also contributes to decarbonization by lessening the frequency at which structures have to be rebuilt, by extending their lifespans.
In addition to the development and production of Basilisk, the Fukushima RDM Center is also using 3D printers to print concrete shapes. Able to make complex shapes that would be difficult using concrete molds, and to shape the concrete at the construction site, they will contribute to significantly shorter construction times and increased productivity in construction and civil engineering. The center is also developing a drone with a large engine that can operate for five hours in a row, which could be used in assisting residents to evacuate in the case of tsunami due to an earthquake, or torrential rains.
◆The tour will visit Aizawa Concrete Co.’s Fukushima RDM Center, and hear from an engineer with the company about the development of the Basilisk self-healing concrete, as well as being able to see where the Basilisk is made and product samples made using 3D printers.
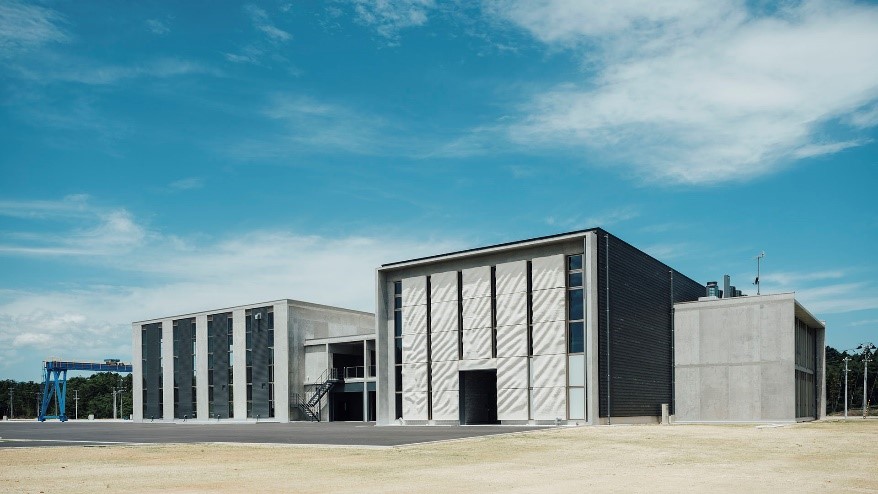
Exterior of the Fukushima RDM Center research lab. Made in a wave shape with a 3D printer, based on observational data of the wind in Namie. 【Photo courtesy of Aizawa Concrete Co.】
*If the 3D printer is in operation, it will be possible to see it but no photography or filming will be allowed.
6. KiMiDoRi Co., Ltd. (Kawauchi)
—Driving forward the recovery of Kawauchi, overcoming the evacuation of the whole village
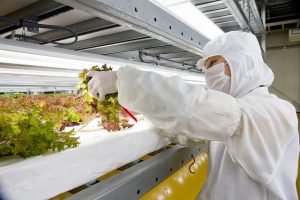
【Photo courtesy of KiMiDoRi Co., Ltd.】
In Kawauchi, Fukushima, a village which had a population of around 3,000 before the earthquake, the entire village had to evacuate due to the Fukushima Daiichi accident, but approximately one year later residents began returning based on the village’s decision.
In 2013, the year after residents began to return, the village government and Matsuno Co., Ltd. (a food wholesaler) jointly funded the establishment of KiMiDoRi Co., Ltd., with the goal of recovering the village’s agricultural industry and creating jobs. By using hydroponic cultivation in a completely closed-off space unaffected by external factors like the weather, they can provide a stable supply of safe and fresh vegetables grown without agricultural chemicals, which can be eaten without even washing them. Since vegetables grown in the factory taste less grassy and bitter, they have received positive reactions from consumers, such as comments from people that dislike vegetables saying they will eat KiMiDoRi vegetables.
The KiMiDoRi factory grows leaf vegetables such as frill lettuce and herbs such as basil in 20 day cycles from planting to harvesting, producing about 3,000 plants per day and around 48 tons per year. Continually improving productivity and optimizing the number of workers, the company’s strength is that it has achieved the most efficient production per kilogram when compared to other plant factories, according to KiMiDoRi’s Ms. Maya Kaneko.
In addition to the vegetables grown at the factory, they have also developed a basil paste made from the basil grown there, and sell that as well. KiMiDoRi has become an employer for local residents now that the nuclear power plant is gone.
◆The tour will visit KiMiDoRi Co., Ltd. and hear from Mr. Kiyoteru Endo, vice-mayor of Kawauchi and KiMiDoRi’s president, and from Ms. Maya Kaneko, head of the KiMiDoRi Production Development Department, about the establishment of the company and the unique characteristics of the factory, as well as be able to see the vegetables being grown in the plant factory.
*Please note that for sanitary reasons, it will only be possible to see/film/photograph the vegetable growing area through a window.
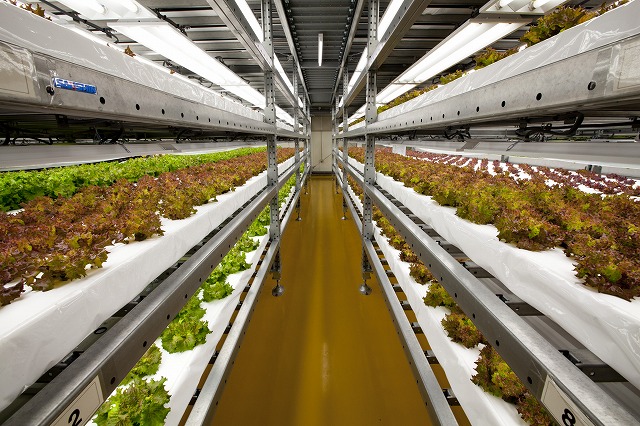
【Photo courtesy of KiMiDoRi Co., Ltd.】
7. National Institute of Technology, Fukushima College (Iwaki)
—Educating the next generation of engineers for the decommissioning of the Fukushima Daiichi Nuclear Power Station. Students developing robots for decommissioning
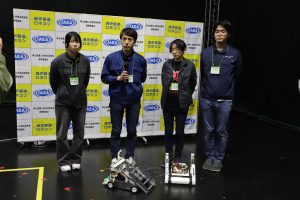
【Photo courtesy of National Institute of Technology, Fukushima College】
Colleges of technology (Kosen) are five-year higher education institutions with the goal of training engineers through specialized education focusing on experiments and practical learning. In recent years, Japan’s Kosen system has also been adopted in Vietnam, Thailand, and Mongolia.
There are approximately 50 Kosen throughout Japan, but the National Institute of Technology, Fukushima College in Iwaki, Fukushima is focusing on educating students in the field of nuclear power, due to experiencing the nuclear disaster. One such initiative is the research and development of robots for decommissioning. Every year since 2016, the Japan Atomic Energy Agency and the Council of Technical Colleges for Human Resource Development for Decommissioning have held the Creative Robot Contest for Decommissioning, in which students from Kosen throughout Japan and from overseas educational institutions compete in Fukushima, and students from Fukushima College have participated in this contest as well.
The Creative Robot Contest for Decommissioning provides competitors with a task simulating part of the long-term decommissioning efforts for the Fukushima Daiichi Nuclear Power Station, and the students build a robot to clear that task, with the intention being to increase students’ interest in decommissioning. In the 9th Creative Robot Contest for Decommissioning held in December 2024, the students from Fukushima College received a Special Award.
One of the original proponents for the Creative Robot Contest for Decommissioning, who advises students at Fukushima College on developing robots for decommissioning, is Professor Shigekazu Suzuki, who says he has felt a gradual decline in interest towards decommissioning from outside the prefecture. Professor Suzuki explains that by providing younger generations with education in the field of nuclear power, they develop an interest and some will become involved in decommissioning. Fukushima College has also begun joint development of robots for decommissioning with a private sector company, and the professor hopes they will reach the stage of practical application.
One of the member’s of the college’s Fukushima Decommissioning Research Club who participated in the robot contest, Ms. Ayuki Tsukada (20 years old, a fifth-year student), had a strong interest in decommissioning since she was an elementary school student, and came from outside Fukushima Prefecture to study at the college. After graduating, she intends to go to university and become involved in developing robots for decommissioning in the future.
◆The tour will see where students with the college’s Fukushima Decommissioning Research Club develop their robots for decommissioning, as well as a demonstration by students who participated in the Creative Robot Contest for Decommissioning. The students will also speak about the results of their research and their passion for developing robots. Professor Shigekazu Suzuki, who teaches at the school, will discuss the importance of educating students in nuclear power.
【Tour Itinerary】
1.Dates
Wednesday, January 29 – Thursday, January 30, 2025
2.Schedule
【Day 1: Wednesday, January 29】
07:12-08:44 |
Tokyo Station→Fukushima Station |
10:30-11:20 |
Briefing by Fukushima Innovation Coast Promotion Organization |
11:30-12:50 |
Zip Infrastructure, Inc. |
13:15-14:10 |
Lunch |
14:30-16:00 |
Aizawa Concrete Co. |
16:30-18:00 |
AstroX, Inc. |
18:30 |
Arrive at hotel (Namie) |
【Day 2: Thursday, January 30】
08:30 |
Leave hotel |
09:00-10:30 |
Kikuchi Seisakusho Co., Ltd. Minamisoma Factory |
11:45-12:45 |
Lunch |
13:00-14:10 |
KiMiDoRi Co., Ltd. |
15:30-17:10 |
National Institute of Technology, Fukushima College |
18:17-20:42 |
Iwaki Station→Tokyo Station |
3. Qualification: Bearer of the Ministry of Foreign Affairs of Japan Press Registration Card (in principle)
*Participants will be determined by the tour sponsor.
4. Cost: 13,000 yen per person, including transportation, accommodation (dinner and breakfast included), and lunches (for both days)
*Information on payment and cancellation fee will be provided to participants.
*Participants will be required to pay their own transportation costs to the meeting place before the tour, and after the tour ends.
5. Participants: Limited to approximately 15 participants.
(Only one reporter or one photographer from each company, but two participants from each TV team will be acceptable.)
6.Please be sure to confirm and agree to the following before applying
6-1. Basic Information
(1) This tour is organized by Fukushima Innovation Coast Promotion Organization and run by the FPCJ.
(2) The schedule is subject to change without notice.
(3) This tour will require participants to bear a part of the cost but is not a profit-making venture.
(4) Fukushima Innovation Coast Promotion Organization and the FPCJ take no responsibility for any accidents, injuries, illness, or other problems which occur during the tour.
(5) There may be some restrictions on photographing and filming at the tour sites. Please follow the instructions of the staff in charge.
(6) This press tour is intended to provide opportunities for news coverage. We request that all participants send a copy of the content of their coverage (article, video, or audio in the case of radio) to Fukushima Innovation Coast Promotion Organization through the FPCJ after their reports are published or aired. When your report is in a language other than English or Japanese, we also ask you to provide a summary in English or Japanese. By submitting your application, we assume that you have agreed to these conditions.
6-2.Handling of Personal Information
When applying for the tour, you agree to the below:
*Regarding the handling of personal information, the press tour sponsors and operators will respect Japan’s Act on the Protection of Personal Information and all other laws and guidelines on the protection of personal information, and handle personal information appropriately.
(1)The tour operators will, when there is a need to do so for the press tour, provide the personal information provided when applying (organization name, personal name, etc.) to other parties in the following cases:
-To arrange travel or insurance through travel agencies (Information provided to: Travel agencies, accommodation operators, transportation operators, insurance companies)
-To ensure smooth operations during the tour (Information provided to: Interpreters, stops on the tour, interviewees)
(2) The tour operators, to ensure smooth operation of the tour, will share the personal names and organization names of applicants with the tour sponsors.
6-3.Recordings by Press Tour Sponsors or Operators During the Tour
When applying for the tour, you agree to the below:
(1) For the record-keeping purposes, the tour operators may film or photograph the tour while it is happening. The copyright holders for these photos or videos will be the tour sponsors.
(2) Photos, videos, or articles of the press tour may be uploaded to websites or social media accounts operated by the sponsors or operators.
(3) The likeness or voice of participants may appear in the abovementioned photos or videos, but you agree to their use by the sponsors or operators.
7. FPCJ Contacts:
Watanabe (Ms.), Yoshida (Ms.)
Media Relations Division
(Tel: 03-3501-3405, E-mail: ma@fpcjpn.or.jp)
◆When applying for the tour, you agree to the following conditions◆
- Press tours have participants from multiple media organizations, and interviews, filming, and photographing are generally carried out jointly. There is no guarantee that you will be able to perform individual interviews or take individual videos at any of the stops on the tour.
- You must follow the instructions of the tour sponsor and operators regarding the tour schedule, timing, and restrictions on taking videos or photos. If you refuse to follow instructions, you will no longer be allowed to participate in the press tour from that point on.