Date : September 11 - 12, 2024
Iwate Press Tour: Passing On Traditional Industries to the Next Generation
post date : 2024.08.20
Tour Dates: Wednesday, September 11–Thursday, September 12, 2024
<Lacquerware, ironware, tansu: New challenges for
historical artisanal techniques in Iwate>
- Iwate, the largest producer of lacquer in Japan: Providing 80% of the domestic lacquer necessary to restore Cultural Properties
- Initiatives to pass on artisanal techniques and train younger generations despite the declining birthrate and aging population
- Making traditional industries into sustainable businesses: Increasing profits by exporting overseas and developing products appropriate for modern lifestyles
Iwate Prefecture is the largest producer in Japan of urushi (lacquer), which has been used as a paint in Japan since ancient times. Lacquer is a natural coating made by refining sap collected from the trunk of the lacquer tree, and can improve the durability of materials due to its corrosion- and water-resistant properties. Since its surface also becomes shiny and glossy after drying and hardening, it was widely used on everything from containers to weaponry, Buddhist statues, and buildings. Its beauty also entranced the European sailors who visited Japan during the Age of Exploration from the 15th to 17th century, and many works made using lacquer were exported to Europe during that period. Marie Antoinette is also known to have been an avid collector of Japanese lacquerware.
However, after World War II, cultivation of lacquer trees declined in Japan, along with lacquer production. Facing pressure from less expensive Chinese lacquer, at one point less than 2% of the lacquer used in Japan was domestically sourced. In 2015, the Agency for Cultural Affairs announced a new policy that in principle, domestic lacquer would be used for publicly funded maintenance and repair of National Treasure and Important Cultural Property buildings. This led to increased demand for domestic lacquer, and Iwate Prefecture moved to increase production. As of 2022, Iwate Prefecture supplied around 80% of domestic Japanese lacquer.
Iwate Prefecture is home to an area that has been producing lacquerware since approximately 1300 years ago, and another area that has been producing traditional tansu (chests of drawers) using lacquer since the 18th century. Due to ample amounts of quality iron being produced in the area, there is also a long tradition of cast iron manufacturing, and it is also known for this Nambu tekki (Nambu ironware). However, with birthrates declining and populations aging throughout Japan, the ratio of seniors (people 65 or older) in Iwate Prefecture reached 35.2% in 2023. A number of initiatives to pass on the techniques of artisans to the next generation can now be seen in traditional industries throughout Iwate Prefecture. There are also efforts being made to develop new products fit for modern lifestyles using traditional techniques, in order to attract a wider range of consumers. There is even a business owner who has significantly expanded exports by actively promoting their goods in overseas markets, in an effort to make a traditional industry into a more sustainable business. By increasing revenue through exports, the goal is to hire younger people and get them involved in the industry, thereby passing on the tradition to them.
◆This press tour will visit traditional industries involving lacquer in Iwate Prefecture and get a close look at artisanal techniques with long histories, as well as interviewing people making efforts to pass those traditions on to the future despite the declining birthrate and aging population, through initiatives such as training successors, developing products fit for modern lifestyles, and expanding sales routes overseas.
[Tour Details]
Reviving Lacquer Production and Restoring Cultural Properties
1. Konishi Decorative Arts & Crafts (Ninohe Branch)
—Training the next generation of lacquer producers in response to growing demand for domestic lacquer due to government policy
https://www.konishi-da.jp/history/ (Japanese only)
Konishi Decorative Arts & Crafts has been maintaining and repairing the ornamentation of temples and shrines for over 300 years, since the 17th century. They remain the largest company in the business today, maintaining and repairing buildings designated as National Treasures and Important Cultural Properties. In 2020, they handled the maintenance and repair work for the Golden Hall of Chuson-ji Temple, a National Treasure located in Hiraizumi, Iwate.
In 2016, Konishi established a branch office in Ninohe, Iwate, the largest producing area for lacquer in Japan. The impetus for the establishment of this new branch was a sudden growth in demand for domestic lacquer when the Agency for Cultural Affairs released a notice in 2015 that in principle, domestic lacquer would be used for maintenance and repair of National Treasure and Important Cultural Property buildings covered by government subsidies. Due to domestic lacquer having become indispensable to Konishi’s primary business of maintaining and repairing Cultural Property ornamentation, acquiring a supply became urgent. Since 2016, Konishi has been carrying out every step of lacquer production itself in Ninohe, growing lacquer trees from saplings, cultivating groves of lacquer trees, and making cuts in the trees to collect the sap that is released.
Since the 2015 notice, there has been increased lacquer production throughout the Ninohe area, which has long been a center for lacquer production. The amount of domestic lacquer produced in 2022 was 1.5 times the amount produced in 2015. Although Japan still only produces 7% of the lacquer it uses, approximately 80% comes from Iwate.
The growing age of lacquer harvesters and lack of successors was a serious issue, but with the 2015 notice from the Agency for Cultural Affairs, producer organizations and local governments have been making efforts to train the next generation to respond to the growing demand for lacquer. As the largest company in the industry, Konishi is also making efforts to hire and train lacquer harvesters, and currently five lacquer harvesters are working at the Ninohe branch as full time employees, who are mainly in their 20s and 30s and some of whom moved there from elsewhere. With steady employment, an environment has been created where the young artisans who will support domestic lacquer production in the future can hone their skills.
◆The tour will visit the Ninohe Branch of Konishi Decorative Arts & Crafts, and hear from the company’s vice-president and head of the lacquer production division, Mr. Tatsutane Fukuda, about the state of domestic lacquer production, the company’s employment structure for full-time employees, and about training lacquer harvesters. The tour will also visit a lacquer tree grove and have the opportunity to film and photograph a demonstration of lacquer sap being harvested by a young harvester.
(In the case of heavy rain, the lacquer tree sap will be washed away and it will not be possible to harvest it, so the demonstration in the lacquer grove would be cancelled. )
[Photos (top left and top right) courtesy of Konishi Decorative Arts & Crafts (Ninohe Branch)]
2. Chuson-ji Temple Golden Hall (National Treasure/World Heritage Site)
—Local lacquer was used to repair a 900-year-old National Treasure
https://www.chusonji.or.jp/language_en/index.html
Hiraizumi was inscribed on the World Heritage List in 2011, with Chuson-ji Temple being being part of listing. The temple was built in Hiraizumi in 1126 by Fujiwara no Kiyohira, the first head of the Oshu Fujiwara clan who ruled the area in the 11th and 12th centuries. Having lost family to war, Kiyohira dedicated Chuson-ji Temple to those who lost their lives on both sides, with the hopes of creating a peaceful utopia without war in this life. Over the next hundred years or so, Hiraizumi prospered as the base for the Oshu Fujiwara clan for four generations.
Within the grounds of Chuson-ji Temple is the Golden Hall (Konjikido), a National Treasure which was built in 1124. Great care was taken in order to have it represent the Pure Land, with gorgeous ornamentation inside and out using materials such as gold leaf and mother of pearl. Coffins containing the remains of the heads of the Oshu Fujiwara clan rest inside to this day. 2024 marks the 900th anniversary of the temple’s construction.
The Golden Hall has been periodically repaired since the Middle Ages. In 1968, large-scale repairs were carried out that involved dismantling the whole structure, but with repeated earthquakes and shrinkage of the wood over 50 years, peeling and cracks in the lacquer and gold foil of the hall became quite noticeable.
After carrying out a survey, repairs to the cracks were carried out in 2020. Konishi Decorative Arts & Crafts carried out these repairs on this irreplaceable National Treasure, using lacquer made in Iwate.
<Note>
No filming or photographing is allowed of the Golden Hall or the Sankozo. Images for use in reporting will be provided to participants at a later date after the tour.
◆The tour will visit Chuson-ji and be guided by the temple’s chief administrator Mr. Kocho Sugawara to see the Sankozo, which has Buddhist statues which use lacquer, and the Golden Hall, as well as hearing about the repairs to the Golden Hall in 2020, and his thoughts on having domestic lacquer used for those repairs.
[Photos courtesy of Chuson-ji Temple]
Lacquerware
Developing New Products/Public-Private Collaboration on System to Train Next Generation
3. Marusan Shikki
—Passing on exquisite artisanal techniques and developing new products to match modern lifestyles
https://hidehiranuri.jp/ (Japanese only)
Lacquerware was made in Iwate since 1300 years ago(the beginning of the 8th century), but in the 12th century the third head of the Oshu Fujiwara clan, Fujiwara no Hidehira, invited an artisan from Kyoto to make a piece using ample amounts of local lacquer and gold. This was the origin of the Hidehira-nuri style, characteristic for having diamond-shaped gold leaf placed atop patterns of clouds, along with lacquer paintings of plants and flowers.
Marusan Shikki, which produces Hidehira-nuri, carries out every step of the process at its workshop, from making the wooden base to painting the final design, and has since being founded in 1904. In addition to traditional lacquerware, the company actively develops new products. In 2002, the fourth-generation owner, Mr. Ichiro Aoyagi, developed a special technique for painting lacquer on glass, and the company used this technique to sell products such as drinking glasses. These products have also been popular with the growing number of foreign tourists recently.
Marusan Shikki has established a new brand, Fudan, which uses a technique to lightly coat wooden surfaces with lacquer in a way that makes it possible for the wood grain to be seen in the finished product. Since it is also less likely to peel than the standard multi-layered coating, and is a simple, interesting design, the brand has been becoming popular with younger generations. As the name “Fudan” suggests (fudan: normal; everyday), the concept of this brand was lacquerware that could easily be used everyday. It was developed by Mr. Takuo Aoyagi, the younger brother of the fifth-generation owner of Marusan Shikki, Mr. Makoto Aoyagi.
While maintaining traditional techniques, Marusan Shikki is also developing easy-to-use products appropriate for modern spaces in order to pass on those traditional techniques to the next generation.
◆The tour will visit Marusan Shikki and hear from the fifth-generation president of the company, Mr. Makoto Aoyagi, about the company and the development of products matching modern lifestyles. The tour will then have the opportunity to film and photograph artisans working on Hidehira-nuri in the workshop, and to hear from Mr. Makoto Aoyagi’s younger brother, Mr. Takuo Aoyagi, a lacquerware craftsman.
[Photos (top right and bottom right) courtesy of Marusan Shikki]
4. Ashiro Urushi Technique Research Center/Appi Urushi Studio
—Public-private collaboration on system for training the next generation in an area with 1300 years of history in making lacquerware
https://www.appiurushistudio.com/en/
Since ancient times, many lacquer trees have grown naturally around the Appi River in Iwate, and as one of the largest lacquer-producing regions in Japan, lacquerware has been made there since approximately 1300 years ago. However, with the widespread adoption of plastic containers after World War II, the lacquerware industry declined, and the number of artisans decreased as well. Facing this crisis, the Ashiro Urushi Technique Research Center was established in the city of Hachimantai in 1983, with the goal of passing on the traditions of lacquerware production to the next generation.
Since its founding over 40 years ago, the center has been training lacquerware artisans. Instead of the classic method of apprentices picking up skills by watching their master, the center has skilled instructors who teach students, making it possible to learn the necessary techniques in only two years. A total of 80 trainees have graduated from the center so far, and they now work around Japan as lacquerware artisans. The center is run by the Hachimantai municipal government, and trainees can learn how to paint lacquer there for free. This is a positive example of a local government taking the initiative to pass on local traditional industries to later generations over the long term, and Mr. Fumitaka Fujiwara, who has taught at the center since its founding, is sure that the center makes a positive contribution to the lacquerware industry of Japan as a whole.
In 1999, Appi Urushi Studio was opened as a place to employ graduates of the center. Four women who graduated from the center make lacquerware here with simple designs that match modern lifestyles. The studio was established by the Town of Ashiro (now incorporated into Hachimantai), and after running the studio as a public-private effort, it is now operated by the Appi Urushi Studio Association. The operations of the center and the studio could be considered a long-term, sustainable initiative carried out via public-private collaboration.
◆The tour will visit Appi Urushi Studio first, and hear from its representative director, Ms. Risa Kudo, about the Appi-nuri style along with an overview of the studio, followed by seeing artisans working in the studio. Afterwards, at the Ashiro Urushi Technique Research Center, the tour will have the opportunity to film and photograph trainees undergoing lessons, and hear from Mr. Fumitaka Fujiwara, who has been teaching there since its founding, about his thoughts on training the next generation in the traditions of Appi lacquerware.
[Photos (top left and top right) courtesy of Appi Urushi Studio]
Nambu Ironware
Exports/Reforming the Creation Process to Train the Next Generation
5. Oitomi
—One third of online sales are overseas. Taking advantage of the growth of overseas markets to make a traditional industry into one that younger generations can join easily
Due to ample amounts of materials such as quality iron and river sand being available since ancient times in the cities of Oshu and Morioka in Iwate, cast iron manufacturing has long been popular, and the ironware made in those two cities is known as Nambu ironware. The surface of this ironware was coated in lacquer to prevent rusting. It has also been proven that water boiled in a Nambu ironware kettle has high quantities of iron in it, and there has been growing interest in its effectiveness as an iron supplement.
The origin of the Nambu ironware of Oshu is said to be from when Fujiwara no Kiyohira invited cast iron artisans from Kyoto in the latter half of the 12th century to make various items such as objects for Buddhist altars. Oitomi, which was founded in Oshu in 1848, began by making tea kettles under the protection of the Date Domain, and is over 170 years old. Oitomi’s fifth-generation owner was a pioneer, becoming the first in the industry to begin exporting Nambu ironware to the US in the 1950s. In the 1980s, the company began exhibiting at international trade shows, and gained popularity in France and other European countries. Since around 2010, they have also become popular in countries such as China which have a strong tea culture.
However, due to this popularity, imitations have begun to be made overseas, and Oitomi is aware of the necessity of providing accurate information to overseas customers. In 2022, the company began operating an online shop with international shipping targeting overseas markets. Over half of Oitomi’s sales come from online shopping, and one third of those sales are from overseas sales, with exports being a major aspect of the company’s business. With the weak yen, exports have been increasing. For overseas sales, the most orders come from the US, followed by European countries such as Germany, France, and Poland, with sales in Asian countries also increasing.
The company’s Miyabi iron kettle, made with a gentle shape and blue coating (see picture below), became instantly famous when Los Angeles Dodgers player Shohei Ohtani, who is from Oshu, introduced it on his Instagram account. Since then, around 3,000 orders have come in for it, and the waitlist is a year long.
The ninth-generation owner of Oitomi, Mr. Kaito Kikuchi, has searched for ways to ensure traditional crafts can survive, and emphasizes the importance of expanding the market by developing new sales routes overseas. In order for younger generations to join traditional industries and learn the skills to be passed on, he believes it is necessary to change the business model to one that can ensure an income.
◆The tour will visit Oitomi, and hear from its ninth-generation owner Mr. Kaito Kikuchi about its products and overseas sales through a cross-border e-commerce site, followed by an opportunity to film and photograph artisans making iron kettles.
[Photos courtesy of Oitomi]
6. Tayama Studio Inc.
— Reforming the creation process itself to make it easier to train the next generation: A new way to train successors
https://www.tayamastudio1.com/ (Japanese only)
The origins of Morioka ironware lay in the early 17th century, when tea was very popular, and the head of the Nambu Domain invited kettle makers from Kyoto to make tea kettles. Afterwards, it was promoted as one of the main industries of the domain, and they began making items for daily use as well, which were distributed throughout the country.
Tayama Studio Inc. was founded in 2013 by Mr. Takahiro Tayama, whose father Mr. Kazuyasu Tayama was recognized as a “Contemporary Master Craftsman” by the Ministry of Health, Labour and Welfare as a traditional craftsman making Nambu ironware. Mr. Takahiro Tayama previously worked in marketing at a company outside Iwate Prefecture, but returned to his hometown of Morioka after the 2011 Great East Japan Earthquake. Apprenticing to his father, he learned how to make iron kettles. Tayama Studio develops products fitting modern lifestyles, and is engaged in a variety of businesses. The company is putting a particular focus on training young artisans.
There are 50 to 60 steps in the process for creating Nambu ironware, and depending on the workshop there may be as many as 100. Traditionally when training to become an artisan, apprentices would need to learn each step completely before moving on to learn the next one, and it could take decades before a single artisan was able to carry out all the steps themselves. However, with modern ideas regarding working, the younger generations are growing more and more reluctant to follow the old training methods. In 2019, Tayama Studio developed the Akai Ringo iron kettle, intentionally minimizing the ornamentation processes so even young artisans could be involved in every step of its creation. According to Mr. Tayama, “By having an individual carry out each step of the process by themselves, they can get see the whole picture. Being able to work while understanding the meaning of each step of the process and acquiring the necessary skills is probably more fitting for the younger generations.”
The Akai Ringo kettles became popular due to their simple and modern design that fits in with modern spaces as well, and are now a hit product with a waitlist of several months.
◆The tour will visit Tayama Studio’s workshop and storefront, and hear from company president Mr. Takahiro Tayama about the development of the Akai Ringo and training the next generation, as well as being able to see young artisans making Nambu ironware in the workshop.
[Photos (bottom left and bottom right) courtesy of Tayama Studio Inc.]
Iwayado Tansu
Traditional Craftsmanship and Finding New Niches
7. Iwayado Kagu Center/Kikuhiro Metal Carvings and Crafts
—Chests of drawers decorated with lacquer and metal work, with over 200 years of history. A new brand combining traditional craftsmanship with the needs of modern lifestyles
https://iwayado-kagu.com/ (Japanese only)
https://www.chokinkogeikikuhiro.com/ (Japanese only)
The origin of Iwayado tansu is said to lie at the end of the 18th century, when the lord of the Iwayado region wanted to escape from the economy relying solely on growing rice, and ordered his vassal to develop some kind of wooden furniture. Using zelkova and paulownia as the base materials, they are known for their thick lacquer coating and fittings with gorgeous metal carvings. The lacquer and metal fittings are said to have a more luxurious shine the more time passes.
At Iwayado Kagu Center, three artisans who have been certified as traditional craftsmen by the national government handmake products such as Iwayado tansu to order according to customer’s requests.
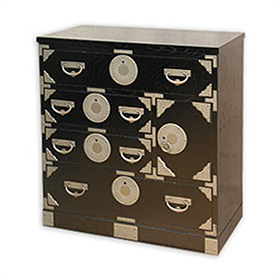
[Photo courtesy of Iwayado Kagu Center]
With the Westernization of living spaces, the demand for Iwayado tansu with traditional designs was declining, but in response to changing consumer needs, they are also making colorful products with modern design sensibilities. The Iwayado Tansu Producer Cooperative, which Iwayado Kagu Center is a member of, has developed the Iwayado Kurashina series based on the concept of “Japanese modern.” Using the same materials and techniques used for Iwayado tansu, the artisans make items such as pen holders, wall clocks, and small containers, which are popular. Products from this series have also been used as gifts for the hometown tax program of Oshu. The Iwayado Tansu Producer Cooperative hopes that a wide range of people will learn of the appeal of Iwayado tansu through this Iwayado Kurashina series, and eventually buy a traditional tansu.
[Photo (bottom left) courtesy of Iwayado Kagu Center]
One of the most representative elements of Iwayado tansu designs are the highly decorative locks and other fittings, which are made by Kikuhiro Metal Carvings and Crafts. One Iwayado tansu has between 60 and 100 metal fittings. They can be made from a variety of materials, such as Nambu ironware or decorative iron or copper plates, but at Kikuhiro Metal Carvings and Crafts, traditional craftsman Mr. Yo Oikawa applies his metal carving skills by using dozens of tools, and carves three-dimensional patterns in metal plates by hand. In addition to carving classic designs which have been passed down since the Meiji period (1868–1912), recently he has also been using his skills on other pieces other than fittings for Iwayado tansu, such as a detailed fitting made based on a picture of a pet and the sign for a store.
[Photos (top left, bottom left, and bottom right) courtesy of Kikuhiro Metal Carvings and Crafts]
◆The tour will visit Iwayado Kagu Center, and see Iwayado tansu being made by traditional craftsman as well as speaking with company president Mr. Shinya Yaegashi about developing the Iwayado Kurashina series. Afterwards, the tour will visit the workshop of Kikuhiro Metal Carvings and Crafts and speak with Mr. Yo Oikawa, as well as having the opportunity to film and photograph him carving metal.
【Tour Itinerary】
1.Dates
Wednesday, September 11 to Thursday, September 12, 2024
2.Schedule
【Wednesday, September 11】
07:32-10:12 Tokyo Station→Ninohe Station (Hayabusa #5)
10:45-12:30 Konishi Decorative Arts & Crafts (Ninohe Branch)
12:45-13:30 Lunch (Japanese Restaurant “Kashiwa”)
14:15-15:45 Ashiro Urushi Technique Research Center/Appi Urushi Studio
17:00-18:30 Tayama Studio
18:40 Arrive at hotel (Morioka)
【Thursday, September 12】
07:50 Leave hotel
09:15-10:30 Oitomi
10:45-12:15 Iwayado Kagu Center/Kikuhiro Metal Carvings and Crafts
13:00-13:45 Lunch (Brewery Restaurant Sekinoichi)
14:00-15:30 Chuson-ji Temple Golden Hall
16:15-17:15 Marusan Shikki
18:38-21:12 Ichinoseki Station→Tokyo Station (Yamabiko #64)
3.Qualification
Bearer of the Ministry of Foreign Affairs of Japan Press Registration Card (in principle)
4.Cost
11,000 yen per person, including transportation, accommodation (breakfast, lunch for 2 days included).
*Information on payment and cancellation fees will be provided to participants.
*Participants will be required to pay their own transportation costs to the meeting place before the tour, and after the tour ends.
5.Participants
Limited to 7 participants.
(Only one reporter or one photographer from each company, but two participants from each TV team will be acceptable.)
*If the number of participants exceeds the capacity, the organizer may make adjustments.
6.Please be sure to confirm and agree to the following before applying
6-1. Basic Information
(1) This tour is organized by Iwate Prefecture and run by the FPCJ.
(2) The schedule is subject to change without notice.
(3) This tour will require participants to bear a part of the cost but is not a profit-making venture.
(4) Iwate Prefecture and the FPCJ take no responsibility for any accidents, injuries, illness, or other problems which occur during the tour.
(5) There may be some restrictions on photographing and filming at the tour sites. Please follow the instructions of the staff in charge.
(6) This press tour is intended to provide opportunities for news coverage. We request that all participants send a copy of the content of their coverage (article, video, or audio in the case of radio) to Iwate Prefecture through the FPCJ after their reports are published or aired. When your report is in a language other than English or Japanese, we also ask you to provide a summary in English or Japanese. By submitting your application, we assume that you have agreed to these conditions.
6-2.Handling of Personal Information
When applying for the tour, you agree to the below.
*Regarding the handling of personal information, the press tour sponsors and operators will respect Japan’s Act on the Protection of Personal Information and all other laws and guidelines on the protection of personal information, and handle personal information appropriately.
(1)The tour operators will, when there is a need to do so for the press tour, provide the personal information provided when applying (organization name, personal name, etc.) to other parties in the following cases:
-To arrange travel or insurance through travel agencies (Information provided to: Travel agencies, accommodation operators, transportation operators, insurance companies)
-To ensure smooth operations during the tour (Information provided to: Interpreters, stops on the tour, interviewees)
(2) The tour operators, to ensure smooth operation of the tour, will share the personal names and organization names of applicants with the tour sponsors.
6-3.Recordings by Press Tour Sponsors or Operators During the Tour
When applying for the tour, you agree to the below.
(1) For the record-keeping purposes, the tour operators may film or photograph the tour while it is happening. The copyright holders for these photos or videos will be the tour sponsors.
(2) Photos, videos, or articles of the press tour may be uploaded to websites or social media accounts operated by the sponsors or operators.
(3) The likeness or voice of participants may appear in the abovementioned photos or videos, but you agree to their use by the sponsors or operators.
7.FPCJ Contact:
Watanabe(Ms.), Yoshida(Ms.)
Media Relations Division
(Tel: 03-3501-3405, E-mail: ma@fpcjpn.or.jp)
◆When applying for the tour, you agree to the following conditions◆
- Press tours have participants from multiple media organizations, and interviews, filming, and photographing are generally carried out jointly. There is no guarantee that you will be able to perform individual interviews or take individual videos at any of the stops on the tour.
- You must follow the instructions of the tour sponsor and operators regarding the tour schedule, timing, and restrictions on taking videos or photos. If you refuse to follow instructions, you will no longer be allowed to participate in the press tour from that point on.